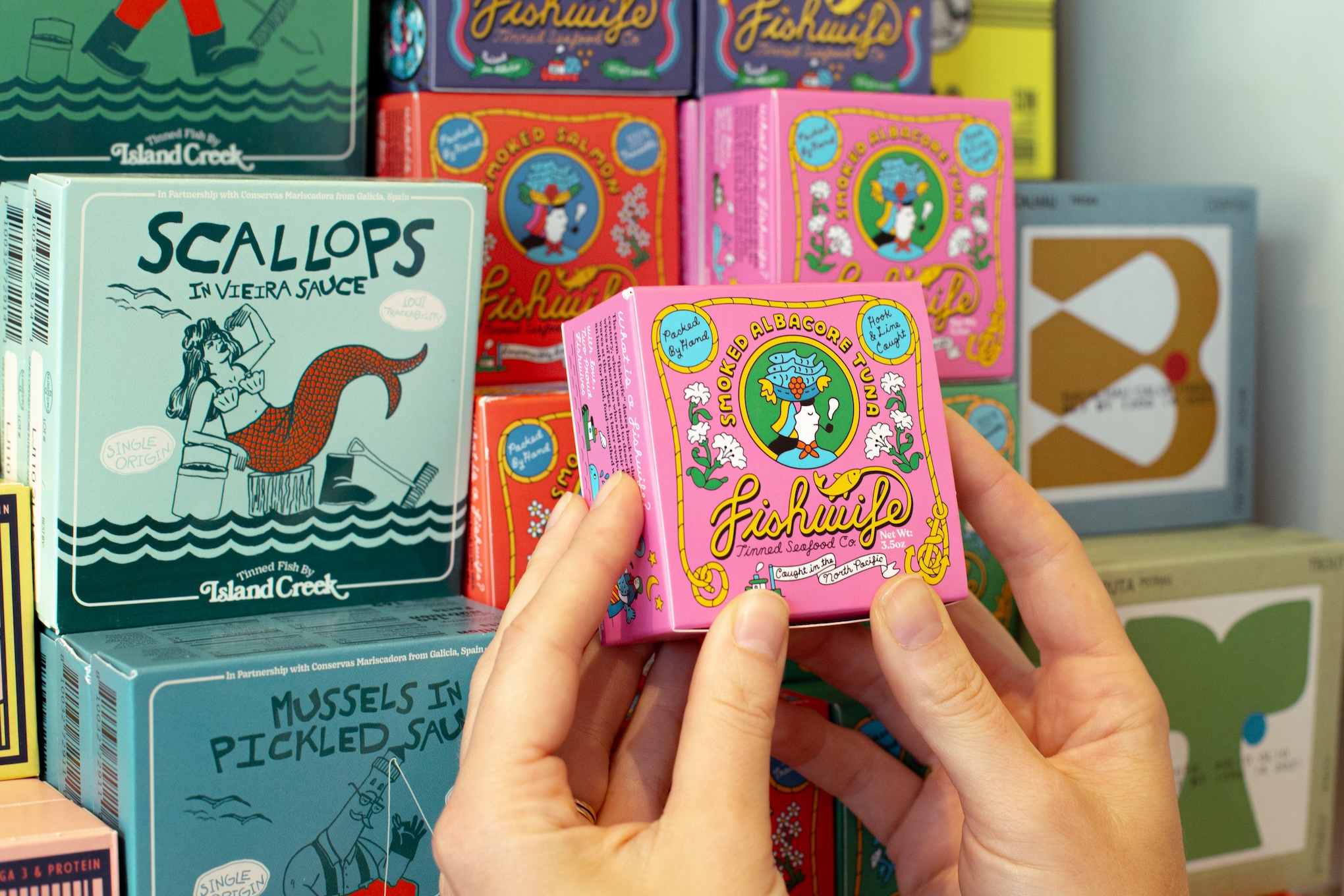
Highlights
- Safety stock ensures that you’ll always have inventory when you need it.
- Businesses need safety stock to keep up with fluctuating demand and lead times.
- The formulas for calculating safety stock are complex, but software can help.
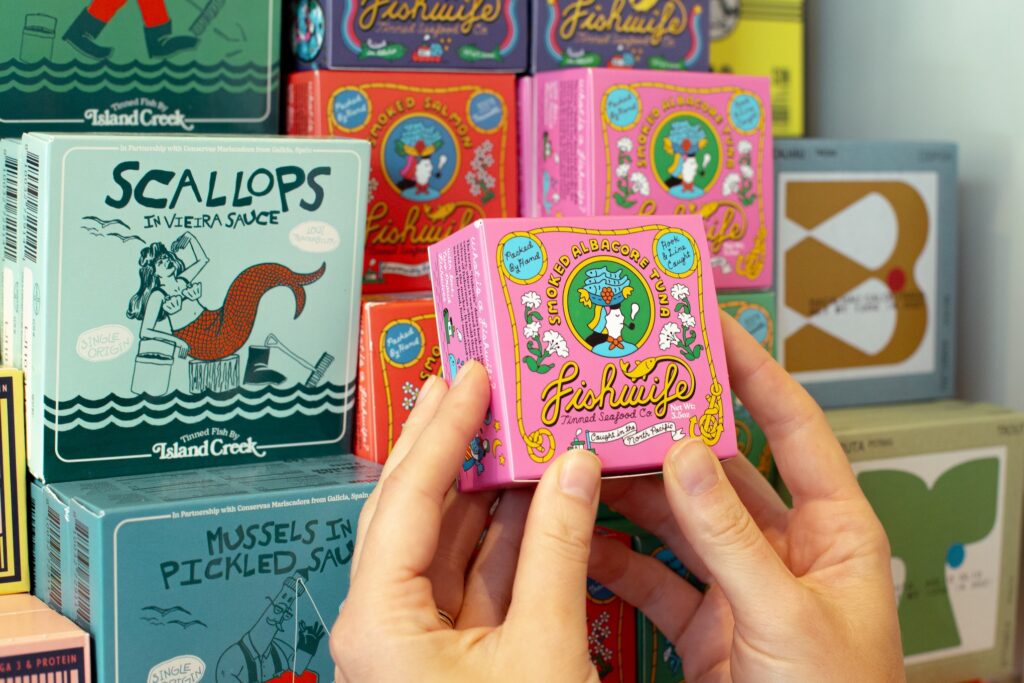
A shopper has landed on your site, eager to add your bestseller to their cart. But wait, what’s this? The dreaded “out of stock” message shows up. Exasperated, they leave your site and search for the item somewhere else. You just lost a sale. This is known as a stockout, and it’s a headache for retailers big and small. Safety stock is the best way to prevent this problem and save you the trouble of disappointed shoppers.
Sometimes stockouts can be unavoidable, but safety stock can stop them from being a common occurrence. Below, we’ll get you up to speed on what safety stock is, why your store needs it, and how to calculate the right amount.
What is safety stock?
Safety stock is the extra stock of a product that businesses keep on hand to prevent stockouts. (Some might also refer to it as buffer stock.) Running a retail business comes with countless uncertainties. Your demand could fluctuate, your supplier could miss a deadline, anything can happen. Before you know it, your inventory turnover rate increases too quickly for you to keep up. Safety stock helps to ensure you won’t get caught without inventory during a critical moment. It’s a safeguard against a shortage.
Why does safety stock matter?
When a shopper tries to order an item and it’s out of stock or, even worse, they successfully order the item but then it’s on backorder for weeks, it can damage the perception of your brand. Say you sell handcrafted artisan jewelry and an influencer wearing one of your necklaces goes viral. You’re thrilled to capitalize on this moment, but you can’t. That’s because your site was flooded with more than 100 orders, but you had only 20 necklaces in stock. Shoppers see your brand as unreliable and move on to a competitor. It’s hard to build trust in a brand when in-demand items are frequently unavailable.
Safety stock protects against four pitfalls for retailers.
- Demand spikes: In the example we described above, the brand experienced a spike in demand that emptied out its inventory and left it high and dry. These spikes aren’t always easy to predict, but retailers often know when their busiest season is or when they have a major social media campaign coming up. For example, if you sell flower crowns and it’s festival season, keep extra safety stock prepared. This cushion allows you to fulfill orders as usual even if you’re getting bombarded.
- Longer lead times: Retailers are often dependent on their suppliers for inventory. But what happens when there’s an unexpected issue with a supplier? Maybe there’s a transportation bottleneck or a production halt. Instead of just five days until the next shipment, you’re looking at 15 days. Now you’re playing the waiting game as your inventory inches toward zero. If you have safety stock, you have a buffer to keep sales going as usual until your supplier is back in action.
- Price fluctuations: If your inventory involves raw materials, you can be at the whim of price fluctuations. If you sell handmade merino wool sweaters and the price of wool suddenly shoots up, you can get stuck paying this inflated price when you need inventory. If you already have safety stock standing by, you can wait out market fluctuations and avoid buying stock when it’s at a higher price.
- Increased shipping fees: If you experience a surge in demand for one of your products or enter a chaotic shopping season, you might need to quickly order more products from your supplier. But since you need the products in two days instead of your usual two weeks, you end up paying a rush fee to your supplier so they can get it there in time to avoid a stockout. These rush fees add up and eat into your bottom line. Safety stock can save you money in shipping fees since you won’t be in a last-minute scramble to get more inventory.
How do you calculate safety stock?
You see why safety stock is important, but how do you know how much you need? Safety stock is more than just keeping an extra pallet of units in the back room. Retailers need to be strategic about calculating the necessary quantity of safety stock. If you have too little safety stock, you aren’t covered in moments of crisis. Order too much safety stock, and you’re stuck paying holding costs for deadstock inventory you may never sell. There are a few formulas to consider. (Keep in mind this isn’t an exhaustive list of how to calculate safety stock, but just a few that are most relevant to small businesses.)
- Basic formula: This short-and-sweet formula looks at the average number of units you sell per day and subtracts the number of days’ worth of stock you want to have on hand. Let’s say you sell 100 silk scarves a day, and you want to always have at least two weeks’ worth of stock on hand because that’s how long it takes to receive stock from your supplier. That means you need to have 1,400 scarves in your inventory at any given time. This formula isn’t completely precise, but it gives you a loose idea of what your safety stock should be, especially if you’re a smaller business.
- Standard deviation formula: This formula can give you a more accurate number than the basic formula, but it’s more complex. When written out, the formula looks like this: Z × σLT × D avg. In this case, “Z” represents how many orders you forecast to get in a set period, “σLT” is your variable lead time within that set period, and “D avg” represents your average demand. (Don’t panic, today’s e-commerce software can help you identify these inputs from your store’s data!) The standard deviation formula is great when you have a lot of variables in your backend or if your store is rapidly growing.
- Reorder formula: A retailer’s reorder point is the moment when they must reorder new stock to avoid dipping into their safety stock. It’s represented as an inventory amount. This formula doesn’t calculate safety stock directly, but it’s an important figure to know when managing your safety stock. It’s written as: Average sales per day x Lead time + Safety stock = ROP, or reorder point. This formula protects your safety stock by letting you know when you should replenish your regular inventory.
- Economic order quantity formula: Your economic order quantity (or EOQ) is the ideal amount of stock you should purchase to reduce your inventory costs. It’s typically written out as EOQ = √DS/H. In other words, you take the demand for the stock (D), multiply it against the cost of those items (S), and then take the square root of that number and divide it by the holding costs for each item. Like the reorder formula, it doesn’t calculate safety stock directly, but it’s an important number to know in order to manage your safety stock.
As you can see, some of these formulas can leave your head spinning. The good thing is no one expects you to calculate these formulas manually! Luckily, there are plenty of software options that will take the sales data and inventory data from your shop and calculate these formulas for you. Inventory management systems Zoho, Unleashed Software, or inFlow Inventory have features that help retailers calculate safety stock by analyzing your demand patterns and lead times. You might check to see if your current e-commerce platform already calculates safety stock for you.
For retailers, maintaining the right balance of safety stock is essential. Safety stock ensures your business continues to run smoothly and reduces the threat of stockouts during high-demand periods. Use the above to discover the formula and software that’s right for your business.